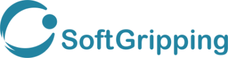
The Modular Design System For Flexible Gripping
In the last years we developed tailor-made solutions for our customers including hygienic design, detectability and rapid adjustment of the gripper in one End of Arm Tooling (EoAT)-device were the result. This customer oriented working routine guarantees the best possible solution. Inspire us with your challenges!
SoftGripper
The grippers for high-speed and cobot applications
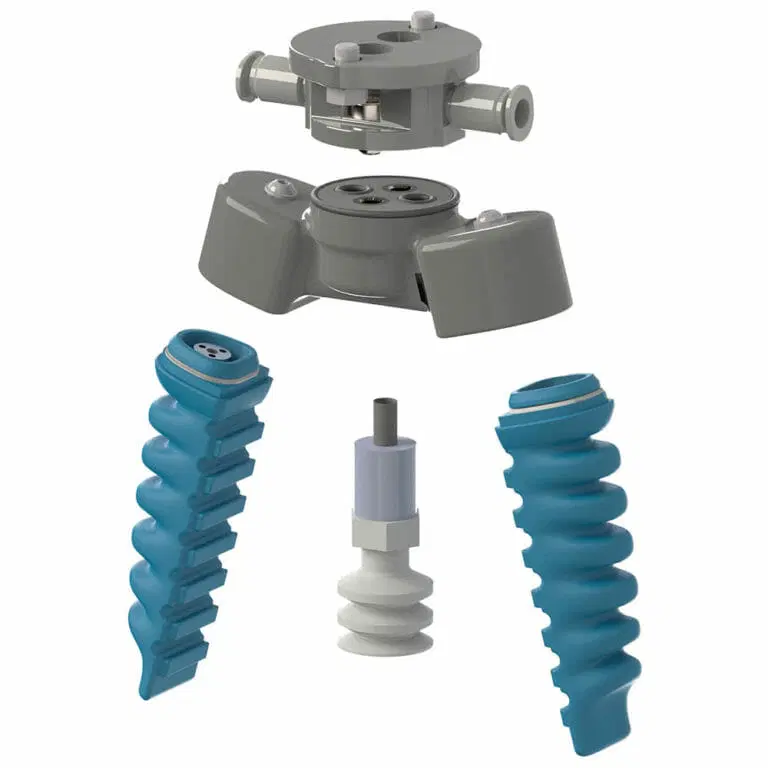
SoftGripper Elements
SoftGrippers are modular. They are made up of multiple elements like: Flange adapter, base, fingers and optionally spacer and suction cup.
Flange and Base
A flange adapter is needed to mount the gripper to the robot. Adapters are available for any robot on the market.
The shape of the gripping object determines the base, which is an essential part of the gripper. A circular object needs a centric base, a cubic or long object a parallel one.
We offer different types of bases with various number of fingers and different angles. Thats fits for the most objects. For special applications, we´ll gladly design a completely individual base for your task in shortest time. The angle of the fingers and the size of the base can be specially tailored to your requirements.
Optionally, our SoftGripping bases are designed according hygienic requirements and can be delivered with a FDA-approved coating.
Fingers
The core of our grippers are the fingers. They adapt to the shape of any object without damaging the surface. The main advantages are the low weight, the speed and the capability to work with all kinds of food. Our pneumatically driven fingers are made of FDA-approved silicon rubber.
Spacers and Suction cups
Suction cups can be used to support the fingers. This is especially useful for bin picking, or when you need additional stabilization of the object. An extention can be used to support the suction cup.
For additional precision and to prevent the goods from sliding up, spacers can be used instead of the suction cup. Or you can use the mount for other tools.
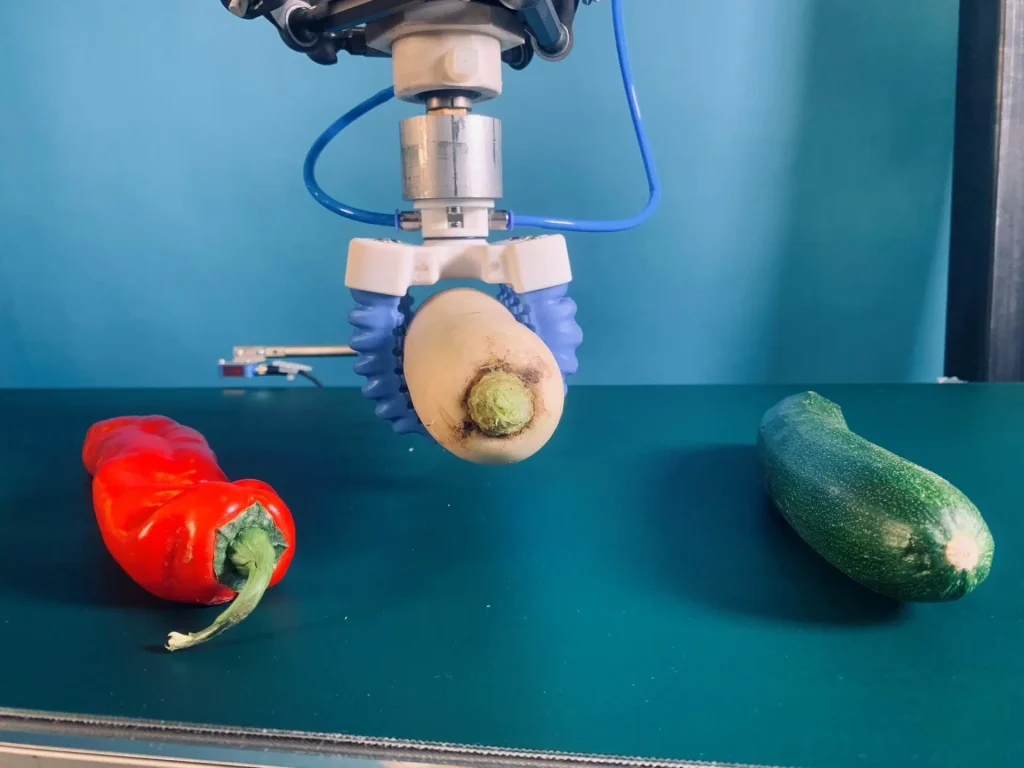
A SoftGripper Is The Best Pick For Any Object And Every Robot
SoftGripping fingers are universal and can be used with any object shape. Primary, SoftGrippers are used in any task involving pick&place using:
- High-speed delta robots
- Scara robots
- Cobots with human interaction
The inherintly superior hygienic design makes cleaning especially easy. For special applications, like handling raw or prepared meats, fish or bakery products, SoftGripper bases are available in special FDA certified coating. This way, cleaning the gripper in a machine or by applying cleaning solutions.
SoftActuator
SoftActuators for your Own High Speed Pick And Place Gripper
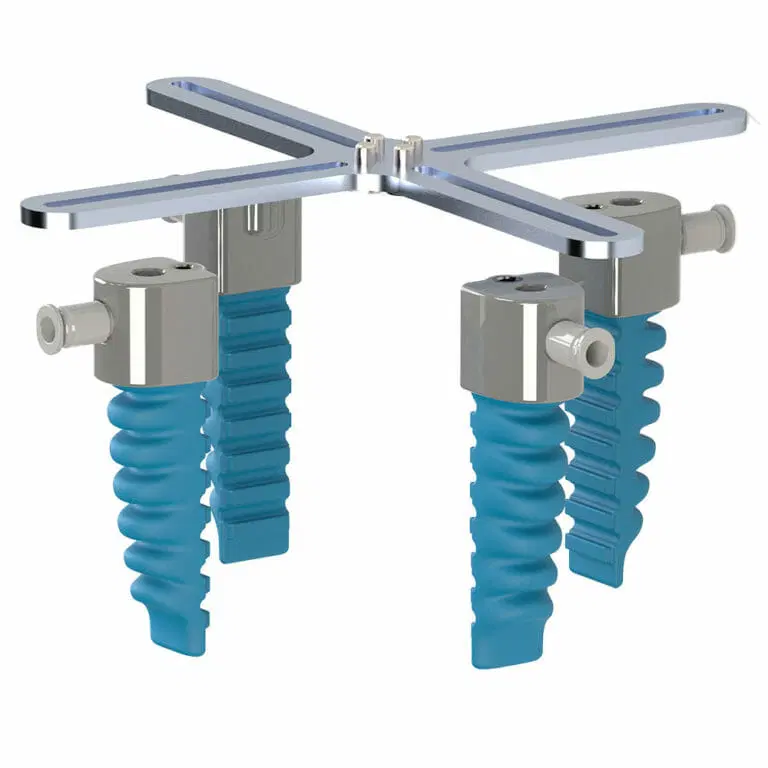
SoftActuator – The Key in automation
- For engineers who wants to build their own Gripper
- For a huge variety of objects
- For easy adjustment when the gripping objects change
- In setups for easy prototyping
Build your own base or use our versatile profiles
We provide the SoftActuators, you choose the shape of your base. This is really special! You can freely choose the type of your base. You like the flexibility of End-of-Arm-Tools (EoAT) systems with aluminum construction profiles? You want to build your own solution with a bended plate (or we can do it for you)? You like to use our versatile profiles? Let’s talk about what you need!
Our SoftActuators are the Fingers for your gripper
Our proven pneumatically driven fingers are made of FDA-approved silicon rubber. You can mount them on every EoAT setup without the need to get a special base. Our SoftActuators are made in hygienic design and materials.
Types of SoftActuators
For maximum flexibility and variability, we offer three different SoftActuators, which are always in stock!
- 1-Finger SoftActuator
- 2-Finger SoftActuator
- 3-Finger SoftActuator
If you need something special like 4, 5, 6, 7, … fingers or actuators with a larger or smaller finger distance, we´ll build it for you within 2 weeks,

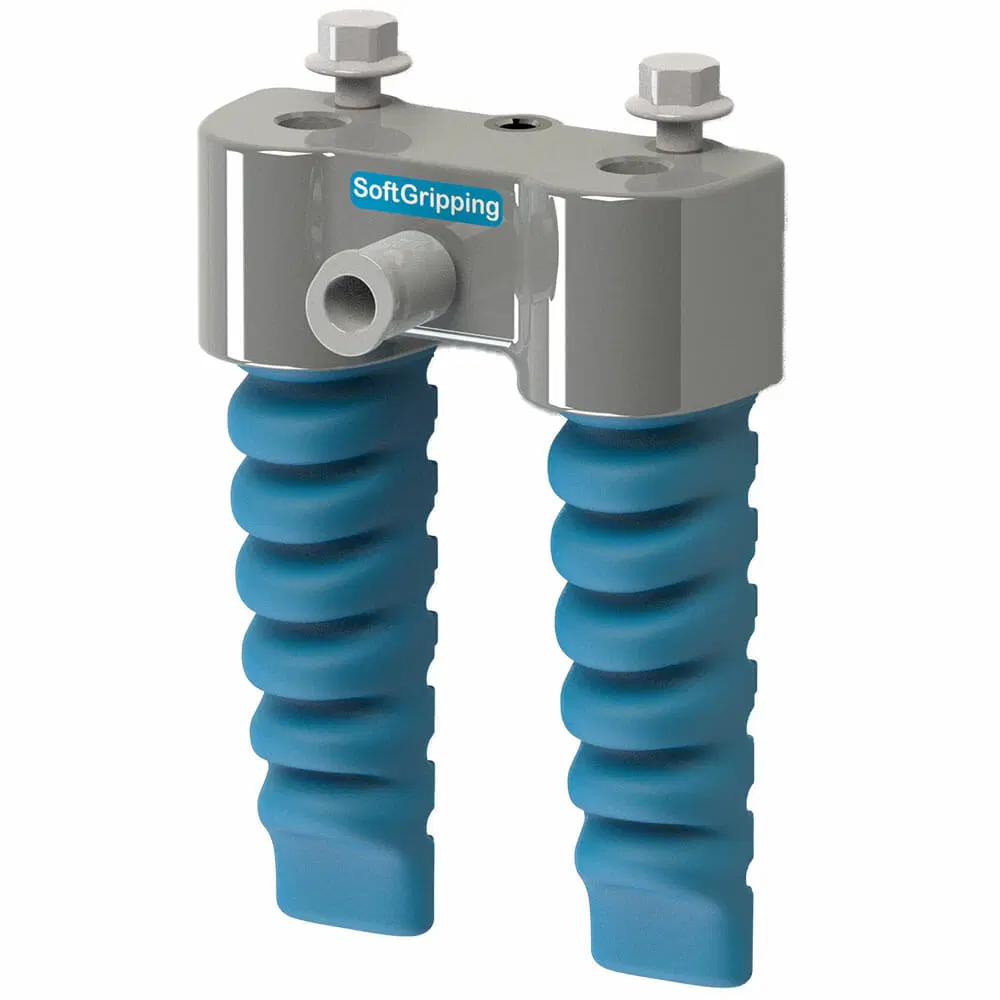
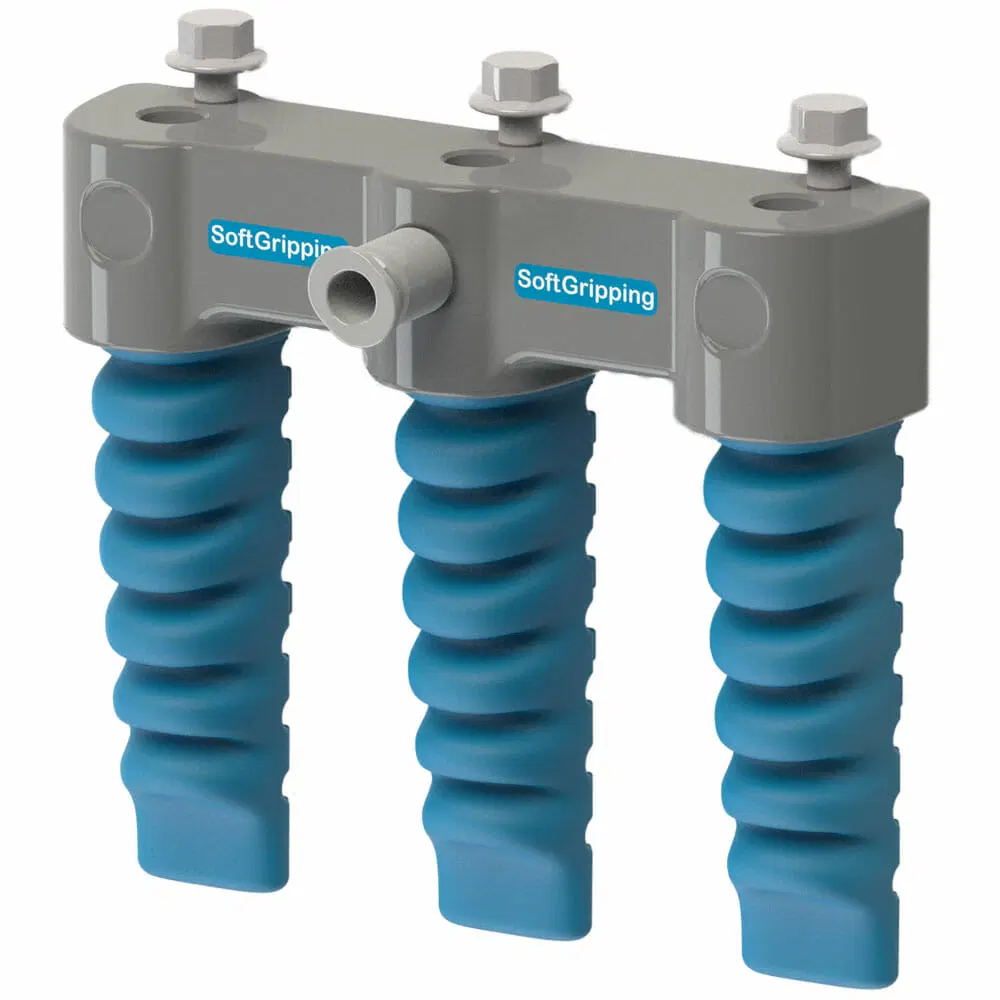
Pneumatics
Choosing the right pneumatics Gripper
Many users who are just starting to automate production and packaging lines are reluctant to use pneumatic gripper instead of electric ones. To demystify the use of pneumatics in SoftGrippers, we decided to summarize all the basic information. The topics can best be divided into the control of the compressor and the fingers.
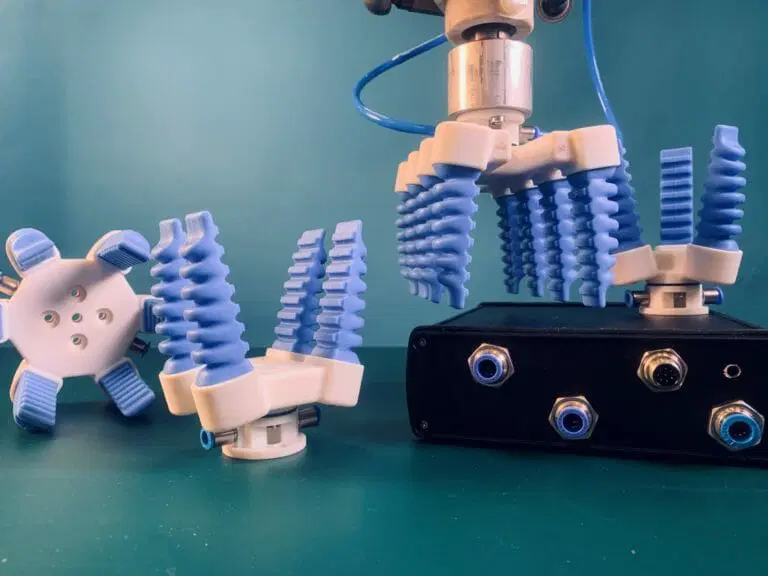
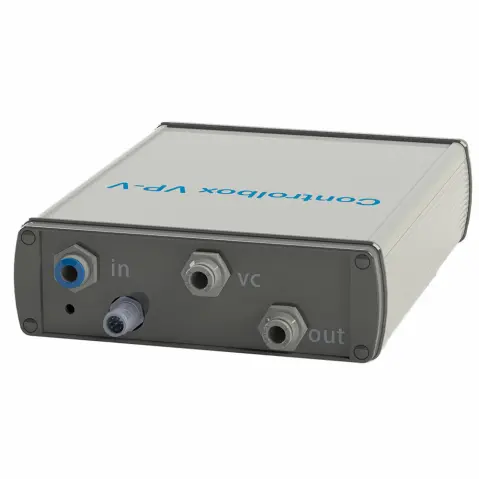
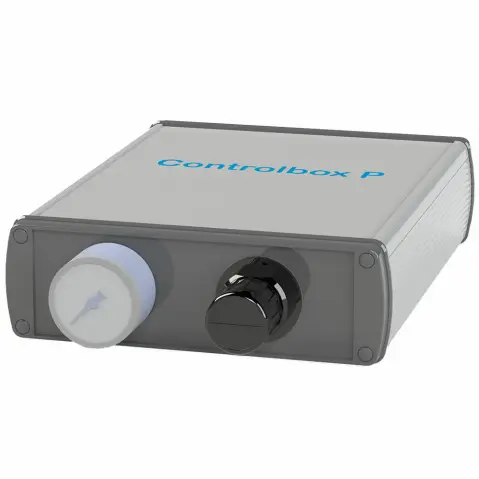
Let’s start with the compressor: Do I need a compressor to operate a pneumatic gripper?
The short answer: Not really!
The long answer: One distinguishes between many applications:
- Mobile applications
- Cobots
- High-speed systems
Since the first two applications only require compressed air for short periods of operating time the fingers and thus the utilization of the compressor is rather low and you can go for a controlbox with an integrated pump. High-speed applications in contrast perform more than 60 cycles per minute. This requires a compressor that is designed for continuous operation and has a larger compressed air tank, which is used as a reservoir. The price difference can be more than an order of magnitude and exceed the cost of the gripper + controller in high-speed automation cases. A Cobot application on the other hand can be operated with an inexpensive and handy pump. So you can really choose between a high-speed controller requiring compressed air, or a all-in-one solution for slower setups. Usually, many penumatic components are used in robotic setups, so if you plan to use a valve battery with your accustomed PLC, please contact our engineers!
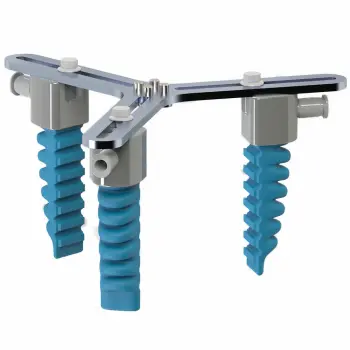
Customer request: We need to change the positions of the fingers fast and without any tools.
Our solution: EoAT plate with hand screws
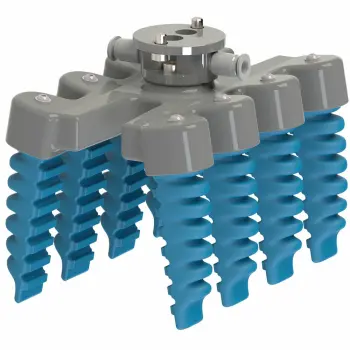
Customer request: For handling raw fish and meat the gripper should be designed according to hygiene standards.
Our solution: Hygienic design, food-grade screws, FDA approved materials and additional coating.
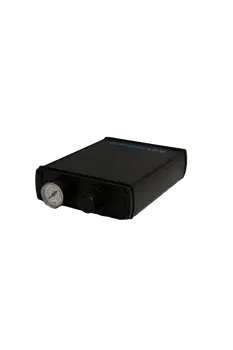
Customer request: The robot in use has only electrical connections. How do we use the gripper in this setup?
Our solution: Our control box offers all required functionalities, including pressure control, pressure sensing and valves.
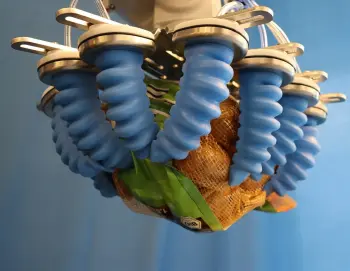
Customer request: A heavy net of potatos needs to be transferred from one lane to another but conventional metal gripper can’t lift it.
Our solution: We developed the GorillaFinger and a custom gripper solution to handle the load.