
ATI INDUSTRIAL AUTOMATION is the world-leading engineering-based developer of robotic accessories and robot arm tooling, including Automatic Tool Changers, Multi-Axis Force/Torque Sensing Systems, Utility Couplers, Material Removal Tools, Robotic Collision Sensors, Manual Tool Changers, and Compliance Devices. Our robot end-effector products are found in thousands of successful applications around the world. Since 1989, our team of mechanical, electrical, and software engineers has been developing cost-effective, state-of-the-art end-effector products and solutions that improve robotic productivity.
ATI MODULAR DESIGN CONCEPT
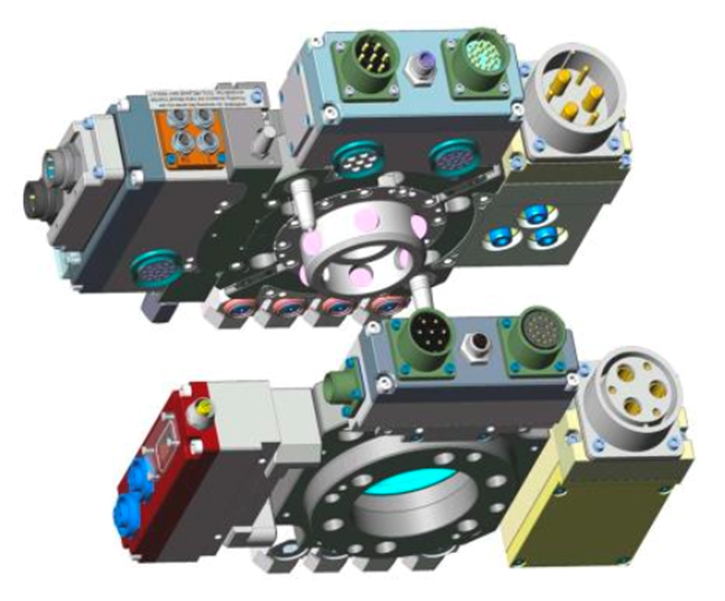
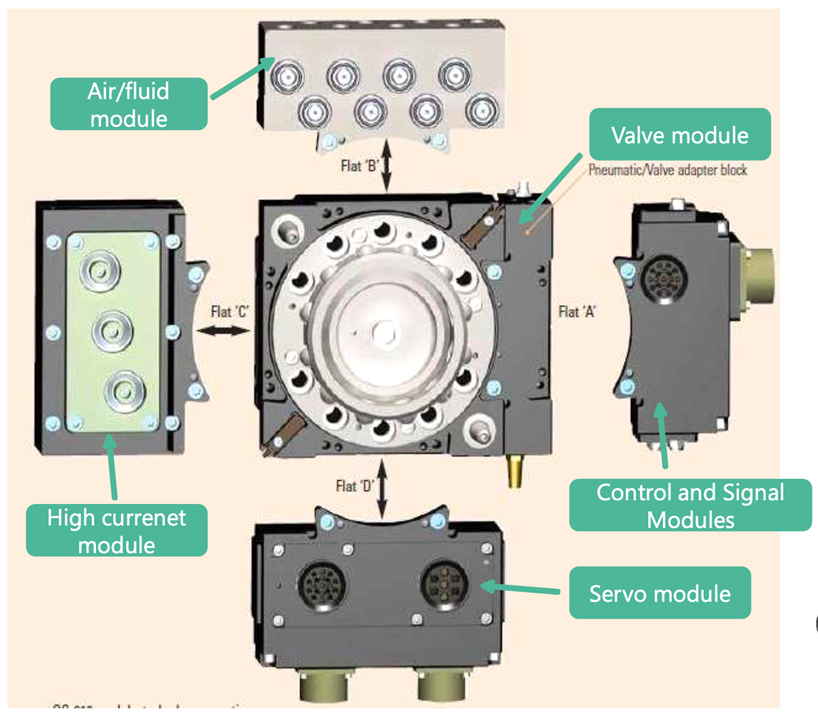
•An anodized aluminum body
•A hardened stainless steel locking mechanism (a cam, male coupling, and chrome steel ball bearings)
•Proximity sensor assemblies used to verify the lock/unlock position of the piston and cam
•Flat A is dedicated for mounting an air adapter or a valve
adapter and control/signal module combination;
•Flats B, C, and D are for optional modules
UTILITY COUPLERS

ATI Utility Couplers are for applications where there is a need to quickly connect utilities such as air, fluid, power and electrical signals in docking and fixturing applications. The modular, multi-coupling design can attach any of ATI’s standard add-on utility modules and will improve cycle-time and flexibility in any production cell. The Master-side connection features a unique rotational compliance mechanism that allows for large tooling misalignments. Utility Couplers can be provided with an electric or air actuated drive cylinder. ATI Utility Couplers offer a quick and cost-effective solution to your challenging coupling needs.
What is a Utility Coupler (UC)?
A dedicated connection device that couples air or electric signals for docking and fixturing applications. A Utility Coupler is typically not designed to carry payloads. Instead, the ATI Utility Coupler includes compliance features that will compensate for severe tooling misalignments. A Utility Coupler is also known as a multi-coupling or quick connector device. A Utility Coupler can be automatic or manual, locking or non-locking, and it can feature compliance or have no compliance, depending on application requirements.
ROBOTIC COLLISION SENSORS
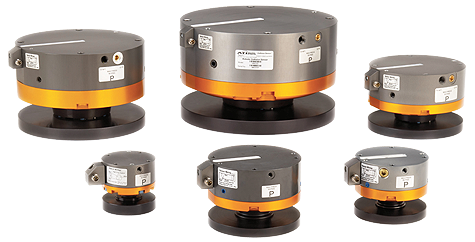
The Protector is ATI Industrial Automation’s patented robotic collision sensor designed to prevent costly damage to robotic end-effectors resulting from robot crashes. The Protector’s features include: automatic reset, high repeatability, large moment rotation, rugged design and low cost.
What is a Robotic Collision Sensor?
Robotic end-effector or device that can detect a crash before or during a collision of the robot or its tool. Also known as the “Protector”, ATI’s Collision Sensor sends a signal back to the robot controller before or during a collision to have the robot avoid or stop the collision. Robotic crash protection devices are Collision Sensors that detect the collision during the crash. A Collision Sensor is also known as a robot safety joint, robot overload protection device, crash protection device, quickstop (trademark of Applied Robotics), robot safety mount, robotic clutch, or robotic collision protector.
MULTI-AXIS FORCE/TORQUE SENSORS
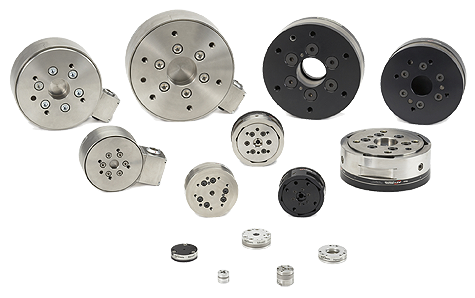
The ATI Multi-Axis Force/Torque Sensor system measures all six components of force and torque. The system consists of a transducer, shielded high-flex cable, and intelligent data acquisition system, Ethernet/DeviceNet interface or F/T controller. Force/Torque sensors are used throughout industry for product testing, robotic assembly, grinding and polishing. In research, our sensors are used in robotic surgery, haptics, rehabilitation, neurology and many others applications. Contact ATI for more information.
What is a Six-Axis Force/Torque Transducer?
A device that measures the outputting forces and torques from all three Cartesian coordinates (x, y, and z). A six-axis force/torque transducer is also known as a multi-axis force/torque transducer, multi-axis load cell, F/T sensor, or six-axis load cell.
Cobot-Ready End-Effector Kits
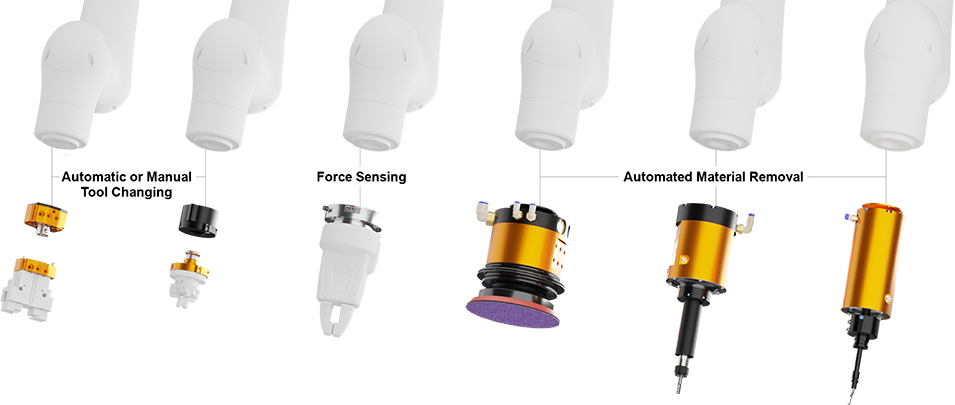
Cobot-Ready End-Effector Kits from ATI offer users a simple and effective way to increase the flexibility of collaborative robots. ATI’s Cobot-Ready End-Effector Kits feature a broad selection of robotic end-effectors that are well suited for an array of industries and application types. These all-in-one packages include options for automatic tool changing, force sensing, and material removal and enable tasks such as assembly, machine tending, part inspection and analysis, surface preparation and finishing, and others to be implemented and executed easily.
Cobot-Ready End-Effector Kits include everything you need to get your cobot application up and running. In addition to the end-effector, you’ll receive all the hardware and software required to connect your system. Within the teach pendant there are simple controls to program your equipment. ATI’s Robotic End-Effectors are designed for robotic use and include design features that make teaching your cobot quick and easy. Cobot-Ready End-Effector Kits are a reliable and affordable way for cobot users to increase process quality and flexibility.
COMPLIANCE DEVICES
ATI offers three unique compliance compensators that allow your workpieces to operate more reliably in tight alignment tolerances with less effort required to design. This will save both time and money, and reduce downtime.
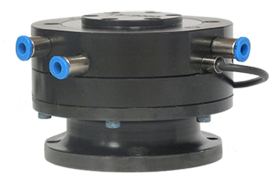
LCC Lateral Compliance Compensator
This unique compensation device offers X-Y lateral compliance and allows pieces to be gripped or routed reliably even if the workpiece is severely misaligned. This unit is designed for high endurance and high repeatability position compensation for use in automated assembly, loading and unloading machines, and more.
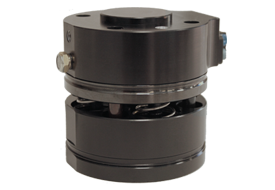
UCC Universal Compliance Compensator
This device is named for its unique combination of compliance behaviors including X-Y Lateral, X-Y-Z Rotation, and Z Compression. After compliance, the UCC returns to center repeatability by means of a pressurized internal reset piston. The compliance stiffness can also be tuned for each application by varying the supply pressure, offering adaptability to a variety of demanding applications including: automated assembly, bin picking, loading and unloading machines, robotic finishing, and more.
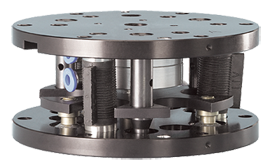
RCC Remote Center Compensators
Designed to correct alignment errors for peg-in-hole automated assembly applications. The RCC Compensator is engineered to project a compliance center (also known as center-of-compliance) forward by using three or more elastomer shear pads. These shear pads are stiff axially and compliant laterally. When the contact point is near the center-of-compliance, the part will automatically correct lateral and rotational misalignment, reducing the contact force and preventing galling and jamming.
MATERIAL REMOVAL TOOLS
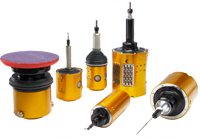
Historically, deburring and material removal processes deploy manual techniques. This is largely due to the limited availability of deburring tools suited for automation. Conventional automated deburring tools exist and perform adequately along a straight line or path, but fail when part tolerances or geometries are not exact. Removing material from a part cavity or protrusion using a robot or other automated process challenges the most skilled of programmers and often leads to inconsistent quality. The Engineers at ATI have developed a family of compliant deburring tools that make automated deburring processes safe, reliable, and affordable. Pneumatic compliance built into these tools exerts a constant force and compensates for displacement. This ensures consistent results and facilitates easy programming.
What is a Material Removal Tool?
A material removal tool is an end-effector used to remove material from a part. ATI’s Material Removal Tools feature integrated compliance and excel in material removal tasks such as deburring, deflashing, edge-breaking, surface finishing, and more. These end-effectors attach to a robot wrist for process-to-part operations, or mount to a bench or fixture for part-to-process setups. ATI’s Material Removal Tools utilize either pneumatic- or electrical-powered motors and offer flexibility with various speed options and compliance ranges.